How bearings work in 7 tips
There are many misconceptions about bearings.
The most common one is that they only work in machines.
This is not true. Bearings can be found in a variety of machines, but they can also be found in other objects.
For example, a car has bearings in the wheel to help it rotate smoothly.
However, bearings are not just limited to machines.
They are also used in everyday items such as pens and even shoes!
Bearings are immensely important components in rotating machinery, as they support and guide moving parts such as wheels, pulleys, fans, and pumps.
Bearings reduce the friction between moving parts by allowing them to move freely along a smooth surface.
They work by creating a cushion between two or more surfaces that reduces the amount of friction generated when these surfaces interact with one another.
The construction of a bearing will vary depending on its application but is typically made from metal materials such as steel or bronze.
These metals provide strength and resistance to wear while also providing low-friction surfaces for the movement of other objects across them.
In this article, we will cover the different types of bearings, each with its advantages and disadvantages.
Some bearings are better for high speeds, while others are better for heavy loads. It is important to choose the right bearing for the job.
How bearings work
Bearings are essential components of many mechanical systems and devices.
They enable rotational motion at the most basic level by providing smooth and frictionless support to moving parts.
When two objects move relative to each other, a bearing allows them to do so with minimal resistance while transferring the load evenly throughout its structure.
This helps maximize efficiency and reduce wear on both the bearing material and the parts it is supporting.
Bearings come in many shapes, sizes, and designs; however, all of them have certain features in common.
At its core, a bearing consists of an inner race containing rolling elements such as balls or rollers that ride between two separators (often called rings).
These rings determine the size and shape of the bearing, as well as its load capacity.
The inner race is typically made from hardened steel or another hard material to withstand wear from repeated contact with the rolling elements.
The outer ring is usually made from softer materials like aluminum or plastic, which help reduce noise levels and friction from contact with other parts within a system.
In operation, the rotating part forces the bearing's rolling elements against the inner and outer races, creating an even distribution of load along its length.
This allows for smooth rotation without damaging the bearing or any other parts within a system.
Additionally, bearings are designed to minimize vibration and noise while in use, which helps with overall performance and reliability.
Overall, bearings provide a reliable solution for supporting the rotational motion and allowing two objects to move relative to each other with minimal wear.
By providing support, reducing friction, and distributing loads evenly throughout their structure, bearings help systems operate more efficiently and last longer.
They also help control noise levels by dampening vibration from contact between moving components.
As such, bearings are essential components in many mechanical systems and devices today.
The history of bearings
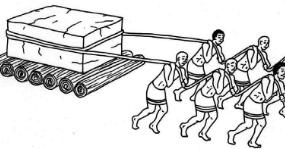
Bearings have a long history dating back to the Industrial Revolution.
The earliest form of bearings, known as bushings, were used in wagon wheels to reduce friction and provide a smooth riding surface for horses.
Later on, during the 19th century, more efficient forms of bearings such as ball bearings began to be used in many industries including automotive, aerospace, and manufacturing.
By the early 20th century, ball bearings had become commonplace in virtually every industry due to their superior strength and load-bearing capabilities.
As technology has advanced over time, so too have the designs and materials used in bearing production.
Today's modern bearings are made from high-grade steel or other alloys that can withstand extreme temperatures, pressures, and loads while still providing maximum efficiency and performance.
As such, bearings remain an important part of the modern industrial and manufacturing process.
In recent years, the use of bearings has expanded into other industries such as medicine, energy, and robotics.
In the medical field, bearings are used in a variety of applications including prosthetics, surgical instruments, and orthopedic implants.
In the energy sector, they help to reduce friction between moving parts in turbines and pumps, while in robotics they are used to provide precise control over body movements.
This increased versatility makes bearings an invaluable tool for modern industry, allowing machines and processes to operate with greater efficiency than ever before.
Furthermore, advances in bearing technology have allowed them to be used in areas where traditional methods were previously impractical or impossible - such as deep sea exploration and outer space travel.
With this newfound ability comes the tremendous potential for future innovation and development.
7 tips for proper bearing maintenance
1. Keep an eye on bearing temperatures.
Temperature is a key factor in ensuring that your bearings are running at their best.
Excessive heat can damage the bearing's internal components and reduce its lifespan dramatically.
As such, it's important to keep an eye on bearing temperatures and address any potential issues as soon as possible.
This could include adjusting the type of lubricant used or replacing worn parts before it becomes too late. By doing this, you can ensure that your bearings will always be able to perform optimally.
2. Make sure the bearings are properly fitted and aligned.
When installing bearings, it is important to make sure that they are properly fitted and aligned with the other components of your system or machine.
If the bearing is installed incorrectly, it can lead to reduced performance or even damage due to uneven stress distribution among its components.
Additionally, improper alignment could cause vibrations which can impact the lifespan of your bearings and reduce their overall efficiency.
It's important to take some time to ensure that each bearing is correctly fitted and properly aligned before use to get optimal performance out of them.
3. Regularly check for signs of wear and tear.
Even if you follow all of these steps, it's still important to regularly inspect your bearings for signs of wear and tear.
This could include checking for cracks, excessive noise or vibrations, or other visual indicators of damage.
If any of these signs are present, you should address the issue as soon as possible to ensure that your bearings can continue to perform optimally for years to come.
4. Keep your bearings clean and free of debris.
Keeping your bearings clean and debris-free is important for several reasons.
First, it can help your bearings run more efficiently, reducing wear and tear.
Second, keeping your bearings clean will ensure that they stay lubricated, which will help them move more smoothly and prevent damage.
Finally, if there is debris caught in your bearings, it can cause them to overheat or even fail. So be sure to keep them clean and free of any junk.
5. If you notice any problems with your bearings, don't hesitate to contact a professional for assistance.
If you have any problems with your bearings, it is important to contact a professional for assistance.
Bearings are essential components of a machine and can wear down over time.
If they are not properly maintained, they can cause significant damage to the machinery.
6. Inspect your bearings for damage or excessive wear.
If you find any damage to your bearings, or if they show signs of excessive wear, you will need to replace them.
Check the manufacturer's specifications for the bearing type and size you will need to replace them.
Take care when removing and replacing the bearings, as improper installation can lead to damage or misalignment of the wheel or other components.
Once the new bearings are installed, check them again for proper fit and lubricate them according to the manufacturer's instructions.
If you feel unsure of this process, it is best to take your vehicle to a professional mechanic who can make sure that everything is done properly.
7. Lubricate your bearings regularly using a quality bearing lubricant.
Bearings need to be lubricated to keep them running smoothly.
It's important to use a good quality bearing lubricant, as this will help to protect the bearings from wear and tear.
Lubricating your bearings regularly can help to extend their lifespan and ensure that they continue to run smoothly.
Additionally, regularly lubricating your bearings can help to prevent the buildup of dust and other particles that can cause them to wear down faster.
With regular lubrication, you can ensure that your bearings continue to perform optimally for years to come.
By following these steps and taking proper care of your bearings, you can be sure that they will remain in optimal condition and perform correctly for a long time.
Regular maintenance and inspection are key in ensuring that your bearings run smoothly and efficiently.
By doing so, you can keep your system running without any issues over its lifespan.
Bearing loads
Bearing loads are an important feature of many types of machinery and structures.
They can be static or dynamic, depending on the application.
To ensure that the bearing can withstand the forces it is subject to, it must be designed correctly according to specific load requirements.
The type of material used for the bearing will depend on these requirements as well as its ability to resist corrosion, wear, and lubrication.
Other factors such as temperature range, speed rating, and axial thrust capabilities may also need to be considered when selecting a suitable bearing for a particular application.
Proper installation plays a major role in ensuring that the bearing's performance meets the required standards.
If not properly installed, it could lead to premature failure or inadequate operation.
Additionally, the bearing must be kept clean and free from debris to ensure optimal performance.
Regular maintenance should also be performed to check for signs of wear or damage, as well as lubrication levels.
In this way, any potential issues can be addressed before they become a problem.
Bearing loads are essential for the successful functioning of many machines and structures, so proper selection and installation are crucial.
With the right design and maintenance routines in place, bearings will continue to provide reliable operation even under challenging conditions.
Different types of bearings
Ball bearings
Ball bearings are used in a variety of industries for their durability, low friction, and precision.
They provide smooth-running motion in machines by reducing the amount of friction between moving parts.
This helps to prevent wear and tear on machinery, extending its lifespan and reducing maintenance requirements.
Ball bearings also have a high tolerance for shock loads, making them ideal for use in high-impact or intense environments such as engines and heavy construction equipment.
Additionally, ball bearings feature exceptional accuracy compared to other types of bearing configurations.
By providing consistent results with minimal variation, they can be used in a wide range of applications requiring precise movement or positioning.
With their combination of strength and accuracy, ball bearings are an essential component in many industries today.
Roller bearings
Roller bearings are an essential component of many machines and structures.
They enable smooth movement between two parts, reducing friction and wear. Roller bearings come in a variety of designs to support different applications.
Radial roller bearings are used for supporting radial loads, while thrust roller bearings are used for handling axial loads.
Tapered roller bearings have conical rollers which can handle both radial and axial loads.
Cylindrical roller bearings are capable of carrying high-speed rotational motion with low friction and excellent stability.
Spherical roller bearings have a self-aligning feature that allows them to accommodate misalignments in the bearing mountings.
Needle roller bearing designs provide a large surface area contact with small cross sections, making them ideal for low-friction, high-speed applications.
Roller bearings are used in a variety of industries, including automotive and aerospace, industrial engineering, construction and mining, food production, and heavy machinery.
Ball thrust bearings
Ball thrust bearings are a type of bearing used in applications with high axial loads, such as those found in helicopters and airplanes.
They consist of two raceways separated by a cage that houses the balls.
The inner race is mounted on an axle while the outer race is mounted in the housing or frame.
Ball thrust bearings offer several advantages over other types of bearings including low friction, high-speed capability, and robustness under stress.
Roller thrust bearings
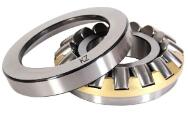
Roller thrust bearings are a type of rotary bearing that can handle heavy loads and have the ability to absorb axial load in a single direction.
They comprise cylindrical rollers, which are arranged radially between two washers.
The rollers are typically separated by cages or spacers and feature a bearing surface that is greater in area than other bearings.
This allows them to handle higher radial and axial loads, making them ideal for applications where heavy loads must be supported.
Roller thrust bearings also possess excellent running accuracy and provide strong load capacity in both static and dynamic conditions.
Tapered roller bearings
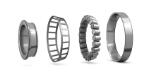
Tapered roller bearings are a type of rolling-element bearing that is most commonly used in automotive applications.
This bearing uses tapered rollers to reduce friction, allowing for the transmission of power from one component to another with minimal wear and tear on the parts.
The design of these bearings also allows them to handle loads that would be too difficult or expensive to manage with other types of bearings.
Tapered roller bearings are especially useful in automotive wheel hubs, axles, transmissions, and differentials due to their load tolerance.
Magnetic bearings
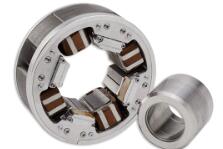
The use of magnetic bearings offers several advantages.
They can be used in high-speed applications, allowing for a much higher rotation speed compared to traditional mechanical bearings.
This allows machines to operate more efficiently and with less stress on their components.
Magnetic bearings also require no lubrication, reducing the need for maintenance and eliminating the risk of contamination from oil or grease.
Additionally, they provide superior vibration-dampening capabilities, which help reduce noise levels and protect sensitive equipment from damage caused by vibrations.
FAQs about bearings
1) What are the factors to be considered before choosing a bearing?
Determining the load capacity and speed requirements for the application, environmental conditions, and accurate description of the bearing.
2) Why is it important to have minimum loads for bearings?
Minimum loads are essential for ensuring that bearings remain in good working order.
Without the application of a minimum load, bearings can develop excessive vibrations, which can cause premature wear and failure.
3) When can oil be applied to bearings?
The best time to apply oil to bearings is when they are installed, as it ensures thorough coverage and lubrication.
Conclusion
The importance of bearings cannot be overstated, as they are essential components in the operation and performance of virtually every machine.
Bearings support moving parts, reduce friction and wear, and increase speed and efficiency while increasing the service life of machinery.
In short, they are essential to efficient functioning machines.